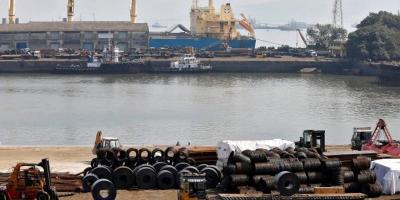
Donald Trump returned to the United States from India a happy man. He inked a $3-billion defence deal with New Delhi, a land which he refers to as a “tariff king”. And all this after the US has terminated India from its Generalised System of Preferences (GSP).>
Under the GSP, which was established by the Trade Act of 1974, policymakers in the US allowed import of around 3,500 products from designated beneficiary countries – primarily low-income countries – at a preferential duty-free (zero-tariff) rate. The idea was to help these ‘poor’ countries increase and diversify their trade with the US.>
The World Bank’s definition of a ‘poor’ or a low-income country is a one with less than $1,026 per capita per annum. India’s per-capita income is around $2,100 per annum. By this definition, Trump is right, and Indian firms need no preferential treatment when it comes to GSP.>
To ascertain how much India loses out from its biggest trading partner because of the withdrawal of GSP, we need to look at the GSP-eligible items, and how much of these items are exported to the US. During 2018-19, bilateral trade between India and the US stood at $88 billion. This makes Washington DC India’s largest trading partner, surpassing China.>
Quick research on the items qualified under GSP suggests these items mostly fall under categories such as textiles and apparel articles, watches, footwear, work gloves, automotive components and leather apparel. India’s exports to the US mainly comprise diamonds (19%), packaged medicaments (14%), automotive components (2.1%) and textile and apparel (3.7%). The numbers in the parenthesis represents the percentage of exports out of India’s total exports to the US.>
Out of these four major export items, few of the items which fall under the textile and apparel categories and automotive components feature in the GSP list. Additionally, organic chemicals, and some engineering goods, such as nuclear boilers, machinery and mechanical appliances are also getting affected from withdrawal of GSP. While the value of these items as a proportion of total Indian exports to the US is quite small, they are one of the fastest-growing exports to the US, registering a growth of 58% between 2010 and 2018.>
Also read: India Was Right to Walk Away from RCEP, But What Comes Next?>
After the GSP withdrawal, there is good news and bad news. The good news is India may not have lost much, with the commerce secretary limiting the loss to $190 million. Only 15 products in the readymade garments sector, contributing to 0.46% of the total garment exports, will now have to face higher tariffs ranging between 0.86% and 14.60% because of GSP withdrawal.>
The bad news? India’s textile and apparel industry is a $150-billion-dollar sector (comprising mainly of micro, small and medium-size firms) that is floundering. The same is the case with the manufacturers of finished aluminium products, especially makers of automotive components and engineering goods. And all of this because of a lack of competitiveness. Indian exports have stagnated between 2010 and 2019. More than the withdrawal of GSP, it is the imprudent domestic policies which are responsible.
India is not only the largest producer of cotton in the world, but also the textile and apparel industry is an industry of national importance when it comes to job creation and exports. This industry employs around 40 million people. An uncompetitive textile and apparel industry is bad news for Modi’s Make-in-India programme and creating jobs. More than the removal of GSP, distorted domestic policies are to be blamed as why this important sector is not performing well.>
Consider this. In India, apparel items below $14 (Rs 1,000) attract a Goods and Services Tax (GST) of 5%. For apparel items exceeding $14, the GST rate is 12%. Even such a lower indirect tax can be detrimental for export competitiveness. For any manufacturer in the textile industry, they also need to invest in value added services such as marketing, warehouse rentals, logistics, courier, and other product fulfilment costs. However, these additional activities attract a GST rate of 18%. This is like the inverted duty structure, as the tax on input is higher than the tax on final output.
The table below shows how a higher GST rate can inflate prices by 4.4%. The government’s failure to rationalise the indirect tax structure is actually costing apparel manufacturers more than the removal of GSP.>
The result is the same whether we consider apparel products less than Rs 1,000 (5% GST) and/or more than Rs 1,000 (12% GST).
Table 1: How GST makes Apparel Industry Uncompetitive>
Particulars | % | Amount (INR) | GST Rate | GST Amount |
Average Selling Price | 600 | 5% | 30 | |
Net Selling Price | 100% | 570 | ||
Less: Costs of Goods Sold on Income Statement | 67% | 382 | ||
Input GST purchase | 5% | 19 | ||
Less: Courier costs | 9% | 51 | 18% | 9 |
Packaging costs | 2% | 11 | 5% | 1 |
Payment gateway costs | 1% | 6 | 18% | 1 |
Marketing costs | 21% | 120 | 18% | 22 |
Warehousing manpower costs | 3% | 17 | 18% | 3 |
Impact on net sell price because of higher GST (18% instead of 5% GST rate) | 4.4 | |||
Particulars | % | Amount (INR) | GST Rate | GST Amount |
Average Selling Price | 1200 | 12% | 144 | |
Net Selling Price | 100% | 1056 | ||
Less: Costs of Goods Sold on Income Statement | 67% | 708 | ||
Input GST purchase | 5% | 35 | ||
Less: Courier costs | 9% | 95 | 18% | 17 |
Packaging costs | 2% | 21 | 5% | 1 |
Payment gateway costs | 1% | 11 | 18% | 2 |
Marketing costs | 21% | 222 | 18% | 40 |
Warehousing manpower costs | 3% | 32 | 18% | 6 |
Impact on net sell price because of higher GST>
(18% instead of 5% GST rate) |
4.4 |
Source: Author’s calculation based on a primary survey. >
The costs related to different value-added services as a proportion of net selling price are collected through the primary survey. Costs of Goods Sold (COGS) is how much it costs to produce goods and include direct material and labor expenses that go into production of each apparel. COGS do not include indirect costs such as overhead and marketing costs.>
For the apparel products, the higher GST rate of 18% as opposed to 5% on value added services have an effect on increasing the net sale price by 4.4%. For the apparel product priced at Rs 600, with a GST rate of 18% the firm has to pay Rs 36 as tax as opposed to Rs 10 as tax when the GST rate is 5%. For the apparel product priced at Rs 1,200, the corresponding figures for tax payment are Rs 66 (with 18% GST) and Rs 47 (with 5% GST), respectively.>
Additionally, the apparel industry which is into exports also suffers from the refund of input tax credit. In March 2019, the government introduced Rebate of State and Central Taxes and Levies (RoSCTL) to refund the input tax. However, apparel industry owners still complain of an inability to get back this refund on account of lack of coordination between the Ministry of Finance and Ministry of Textiles.>
Combine this fact with a higher GST, and it adds on to the cost by as much as 8%. >
Also read: What Will Be the Spillover Effects of the Coronavirus on India Inc?>
The story is the same for manufacturers of aluminium automotive components. Aluminium automotive parts are finished products which are made with raw aluminium. There are three primary producers of raw aluminium in the country, two in the private sector (namely, Hindalco and Vedanta), and the third one is in the public sector (Nalco).>
These three big players control over 90% of the raw aluminium market in India. The government of India has protected the raw aluminium industry by imposing a custom duty of 8.35% (basic plus ad valorem duty) which makes Indian manufacturers producing final aluminium products such as automotive components less competitive in the world market. >
Additionally, the GST rate on aluminium automotive products is 28%, which is the highest GST slab rate. The high GST structure lowers the trade margin for the makers of aluminium automotive product. This makes the business unsustainable even in the domestic market. For example, Chinese governments give 16% subsidy to manufacturers of final aluminium automotive products making the Chinese firms competitive in the world market. >
At a time when China is subsidising its manufacturing activities, it is no surprise why Indian garment manufacturers and makers of aluminium automotive products are going to lose out in the world market. Trump is wooing big industrial groups such as Reliance, Mahindra, TCS, etc. to create jobs in the US. For India, the time has come to hand-hold the small, micro and medium enterprises to create jobs, maintain our export competitiveness and enable them to participate in the global value chain. >
Nilanjan Banik is Professor, Bennett University, Greater Noida. He can be reached at nilbanik@gmail.com.>