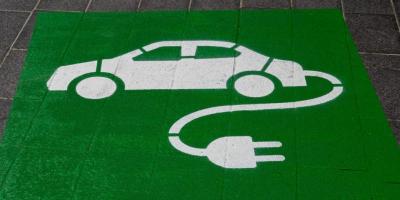
This is the third and final article in a three-part series. Read the first and second parts. >
One starting point of this tale is lithium-ion cells. They were first commercialised by Sony, which was looking to make its camcorders lighter. The technology moved next to Korean firms like LG and Samsung, which extended their use into mobile phones. Then came China. It, too, learnt how to make cells through reverse engineering and joint ventures. Along the way, lithium ion’s use cases expanded yet again – to now include electric vehicles.>
On this hinges the eventual question of how much demand there will be for critical minerals.>
Around the Beijing Olympics, China began subsidising EV buyers. In tandem, it switched public procurement of taxis and buses to EVs and got provincial governments to stump up capital for lithium mining and refining for EV batteries. Localisation also became a focus. To win subsidies, cars had to be locally made, with components manufactured in China.>
Today, the country is an EV powerhouse. Not only does it control the raw materials needed for making electric vehicles but it also has expertise in processing and refining them as well as in manufacturing end-use applications such as batteries and electric vehicles.>
Today, other countries are trying to reprise China’s success. The first part of this series spoke about the US Inflation Reduction Act. Another proposed bill in the US includes a $20-a-kilogram credit for US-made magnets. Manufacturers sourcing 90% of their component parts from US producers could be entitled to a $30-a-kilogram credit.>
India, too, has taken a similar approach. In the mobility sector, through schemes like FAME, it has subsidised EV buyers. The country is also pushing the use of electric buses in public transport. And, with the Production Linked Incentive Scheme (PLI) scheme for advanced chemical cell batteries, the country is trying to create an indigenous value chain for batteries.>
Creating an indigenous value chain>
In May, CarbonCopy asked Union government advisor Randheer Singh about these schemes. Till June this year, he worked as director (e-mobility) and senior team member (advanced chemistry cells programme) at Niti Aayog. He left NITI to start his own outfit.
“FAME is a demand incentive,” he said. “In the past decade, all countries have created such schemes to bring about behavioural changes.” In tandem, he said, the country has rolled out the PLI scheme for batteries. “These companies will have to ensure localisation,” he said. “In the next two years, they have to ensure a minimum of 25% localisation in their batteries. Five years after the award of the contract, localisation has to rise to 60%.”>
In other words, they will have to use locally-made cells, which in turn will have either locally-made CAM, electrolyte or anode. “With PLI, the push is to start making cells in India,” said Uttam Sen, the co-founder of e-TRNL Energy, a Bangalore-based startup trying to make cells in India. “The next push will be to make cathodes, anodes and electrolytes in India.”
That is not all. India is also seeing companies outside PLI invest in battery manufacturing. “There is another lot coming up in ACC [Advanced Chemistry Cells] without government incentive for cell manufacturing,” said Singh. “But these companies, who don’t have localisation targets might not localise the critical components.”>
To get them to localise, too, the government has doubled the basic import duty on lithium-ion cells to 10%. As for battery packs used in electric vehicles, the import duty has been tripled.
This is similar to the steps taken by the government to boost local manufacturing of solar panels. To reduce the country’s reliance on China – and to boost local manufacturing of panels – stiff import duties were slapped on imported panels. This, however, created an outcome where developers said they wouldn’t be able to meet India’s ambitious RE targets.>
And so, how is this approach working in the context of EVs, one of the biggest users of critical minerals like lithium?>
Can India source the technology?>
As this article was getting written, two announcements stunned EV sector watchers.>
First, at a time most lithium-ion batteries have an energy density below 300 watthours/kilogram, CATL unveiled a battery that stores 500 wh/kg. This battery, it said, will be useful for electric flights as well as boost EVs’ range to 1,000 km per charge.>
An even more staggering announcement followed in the subsequent weeks. This one was from Toyota, long under attack for delaying a switch to fully EV models. Early in July, the company announced it had developed a solid state battery that would give EVs a range of 1,200km and a charging time of 10 minutes or less.>
Even as India tries to create its own indigenous EV supply chain, it’s starting late. Other countries have taken large leads in technology and manufacturing – of processing minerals as well as developing the end-use applications for them.>
Also read: Electric Vehicle Policies of States Leave Much To Be Desired: Report>
In response, most Indian firms are bringing in know-how through acquisitions. Reliance, for instance, has picked up tech startups like Faradion (sodium-ion) and Lithium Werks (cobalt-free Lithium-ion). Ola acquired Dutch electric scooter-maker Etergo. Earlier, Tata brought in know-how about EVs through acquisitions like Land Rover.>
As this article gets written, groups like Reliance and JSW are jockeying to pick up a majority stake in Chinese firms like MG Motor. “Companies with links to China have been facing hurdles in getting approvals for fresh investments due to rising tensions on the India-China border,” reported Economic Times.>
According to the paper, MG India has been awaiting government approval for around two years to raise funds from its parent. “With little success so far, it has now started looking for other options to raise the required capital,” it wrote. BYD, too, is facing similar hurdles.>
According to Economic Times, MG Motor is also wondering if it should make hydrogen fuel cells and battery cells in India.>
How such an arrangement is expected to work is clear enough. MG will source tech from its parent – and manufacture in India. Once such companies are compelled to make in India, the manufacturing know-how will spread faster.>
Such joint ventures are how China, too, has acquired manufacturing know-how. Given the large size of the Indian market, it’s safe to assume that foreign makers will come. The country wants them to get their vendors along. As this article was being written, news came that Tesla has asked its battery suppliers to start talks with the Indian government to set up battery manufacturing units in the country. Panasonic Energy, reported Business Standard, has already approached the government.>
Will Indian battery makers source components locally or import?>
This is where the big question lies. Will these plants manufacture battery components in-house? Or buy from an Indian firm like Altmin or E-TRNL? Or focus on assembling batteries from imports? These choices will determine the quantum of critical minerals India will need.>
The first option, as a Hyderabad-based energy consultant had told CarbonCopy last year, will call for further investment. If a firm making solar panels or batteries has to also make polysilicon or cells, will it be competitive against vertically integrated rivals like CATL, which has much more scale? Or would such a firm be better off sourcing components from firms focusing on one rung of the supply chain—like polysilicon, cathode or anode?>
It’s pertinent to say that such firms are coming up in India. Altmin wants to make CAMs. Others like BASF and Epsilon want to make anodes. E-TRNL wants to make cells. Firms like Fashmo are focusing on battery management systems (BMS).>
At this time, both battery plants and those making components for them are struggling with low volumes.>
Take EVs. While India has ambitious targets for EVs, its incentives for EV sales are on the lower side. FAME-II, with an outlay of Rs 10,000 crore between 2019 and 2022 (which was later extended to 2024), wanted to subsidise 7,000 e-buses, 5 lakh e-3 Wheelers, 55,000 e-cars and 10 lakh e-2 Wheelers. To put these numbers in perspective, the number of buses sold last year in India stands at 49,500; 3 wheelers, 767,071; cars, 36,00,039; and 159 lakh 2-wheelers.>
In this landscape, EVs accounted for just 4% of overall two-wheeler sales in the country. This situation has been further warped by the cut in FAME subsidies for electric two-wheelers.>
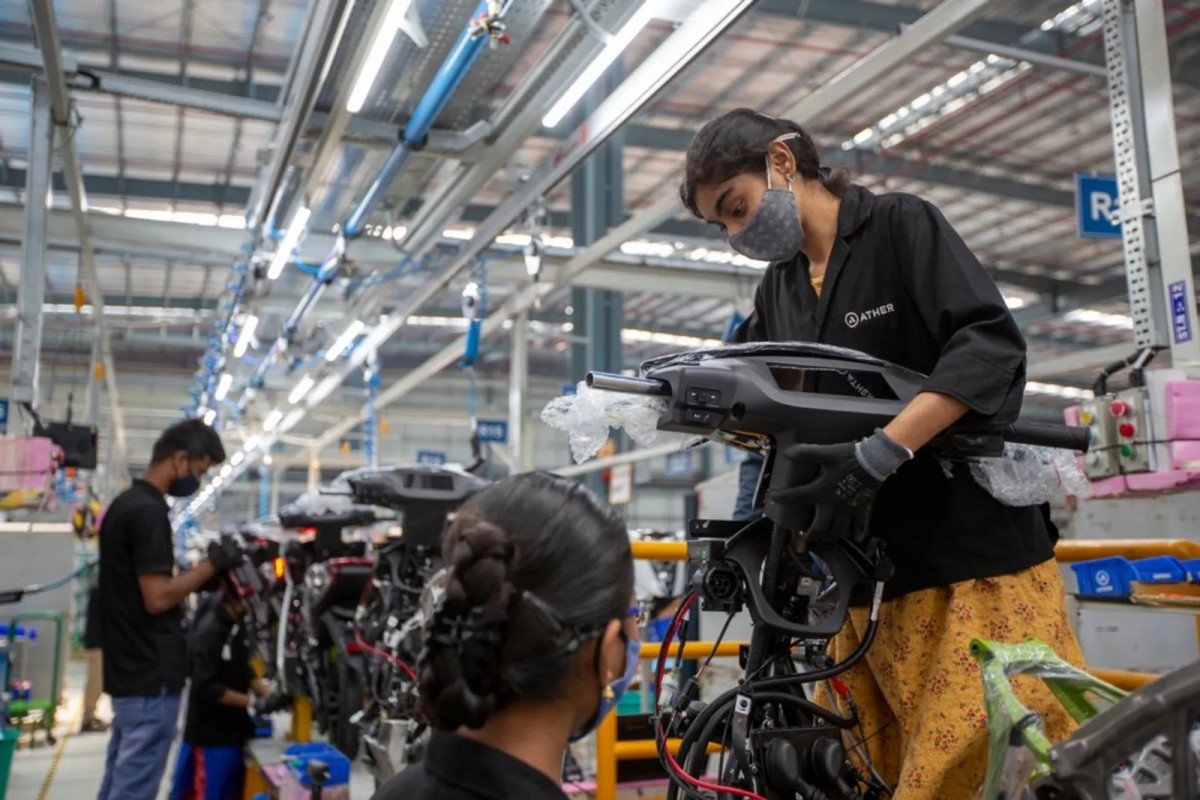
Workers assemble electric scooters at the Ather Energy factory in Hosur, India, April 20, 2022. Photo: Thomson Reuters Foundation/Vivek Muthuramalingam>
“While India has vision statements on the quantum of battery storage the country will need, these are not backed by national EV targets yet,” said Swati D’Souza, energy analyst at IEEFA. “And so, firms are investing, but slowly. They would rather source cathode than set up a cathode factory.”>
Given this uncertainty, a clutch of EV manufacturers continue to merely assemble in India. What does this mean for EV component companies coming up in the country? “Even if I make CAM in India, companies might want to buy from China,” agreed Sunkavalli. “They have more scale.”>
In response, startups are looking overseas for growth. Take Epsilon. The anode maker is boosting its production capacity in India to 10,000 TPA. It’s, however, setting up a 50,000 TPA unit in the US, enough to power a million EVs. Or take the Tata Group. It’s setting up a 20 GWh lithium ion cell manufacturing plant in India – and a 40 GWh battery plant in the UK.>
They are also looking to export from India. “Covid has taken its toll on China’s reputation,” said the promoter of an EV component maker on the condition of anonymity. “No one wants a supply chain shock. At the same time, a trade war is underway.” For this reason, he said, “Countries like Japan are under pressure to find cell manufacturers outside China.”>
This is the China Plus One approach. “If you look at Chinese manufacturers like BTR and Shanshan Energy, they make CAM for about $20/kilo,” Varma had added. “While our scale is very low, our cost will come to about $24-25. That is a premium European and Far-East companies say they are very willing to pay, to secure alternate supply chains outside of China.”>
Apart from delivering growth, this focus on export markets serves another end. “(Firms) should go through this process,” said Rahul Walawalkar, the head of India Energy Storage Alliance. “Selling in global markets is the best way to show that their product is competitive.”>
The bigger question>
And so, how is India’s search for atmanirbharta in critical minerals unfolding?>
As this series has shown, it’s impossible to give a categorical answer to that question. Too many pieces of this puzzle – geopolitics, India’s capacity to source critical minerals supplies, local demand for end-use applications like battery components—are in a state of flux.>
Between recycling, domestic exploration, the mineral security partnership, and India’s own outreach to countries like Australia, the country seems to have multiple pathways for securing its critical mineral supplies.>
And yet, take a closer look and questions emerge. While working on this report, CarbonCopy was told by an industry observer on the condition of anonymity that many manufacturers do not want to stray beyond their core functions of manufacturing and engineering into the messy world of critical mineral mining. And so, will private companies want their own mines or will they be happier with an intermediary – KABIL or global traders like Glencore – supplying critical minerals to them?>
There are other questions. Does KABIL have the resources (staffing, budgets and diplomatic support) to compete with other countries? How is India placed vis-a-vis critical minerals’ refining technologies? How will the Mineral Security Partnership work – and what will be India’s role within that? What parts of the manufacturing chain will come to India? As the sole developing country in the partnership—one with lax environmental regulation, additionally – might India end up being the most polluting parts?>
And then, there are the questions that surround demand. Can India create enough demand – across renewables, grid storage, EVs – to create an indigenous manufacturing sector that absorbs these critical minerals? Without that, firms will keep importing components—and the country’s dependence on other nations will remain.>
And so, how are the firms which won the PLI for rechargeable batteries faring? How fast will the market for EVs grow? Unlike steel which, threatened by measures like carbon border taxes, is going green, India’s automotive cluster is still unsure how rapidly the domestic market will decarbonise. It wants to invest cautiously. Caution, however, comes with its own risks. As other countries – especially those with booming EV markets – invest in batteries and battery components, the minimum viable scale for plants is rising fast.>
Hardwired into all this is also the question of technology. Will Indian units sourcing technology through joint ventures or developing it inhouse as scrappy startups be globally competitive? How will the entry of firms like BYD (even with a local JV partner) and Tesla change this landscape? EVs might get a boost with these firms’ entry but how much of their supply chain will they localise?>
India’s search for critical minerals is no ordinary puzzle. It’s a puzzle with shape-shifting pieces.>
Wait and watch.>
This article was originally published on CarbonCopy.>