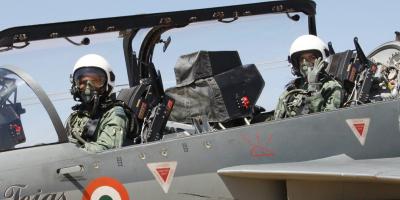
India ventured into the development of many critical technologies post-independence. It successfully designed and flew its indigenous fighter aircraft, HAL HF-24 Marut, launched Satellite Launch Vehicle-3 (SLV-3) and went atomic with its first nuclear device. There have been a few setbacks, a notable one being India’s attempt to develop an aero-engine. In the current geopolitical landscape, the criticality of aero-engine technology is more pronounced. The Defence Research and Development Organisation (DRDO) chief, Samir V. Kamat, underscored this and identified aero-engines as India’s priority at the 21st Subroto Mukherjee Seminar on January 7 in Delhi.>
Even though aero-engine technology is over seventy years old, it is still considered state-of-the-art, and only a handful of nations can design and manufacture it. India aims to become self-reliant in aero-engine technology through the Kaveri Engine programme. To realise this ambitious goal, India must address the challenge by establishing a robust foundation, prioritising institutional transformation, building a collaborative ecosystem, and investing in critical infrastructure.>
Aero-engine technology>
An aero-engine, also popularly known as a jet engine or gas turbine engine, is a highly efficient power source which has revolutionised modern aviation. For decades, this capability has allowed humans to fly fifty to sixty thousand feet above sea level and as fast as the speed of sound. This innovation has made air travel more affordable and accessible to the common populace. The inventors Frank Whittle and Hans von Ohain developed the aero-engine to eliminate the drawbacks of the piston engine used to power aircraft before the 1940s. Other technologies, like rockets or nuclear, exist but are currently unsuitable for aircraft power sources. With the advancement in electric propulsion, smaller VTOL (Vertical Take-Off and Landing) aircraft are powered by electric engines. However, they cannot replace aero-engines for commercial jetliners and military aircraft in the foreseeable future.>
The complexity of this engine arises from the extreme environment within its internal operations. Key components like high-pressure turbine blades rotate at a staggering speed of ten to fifteen thousand rpm (rotation per minute) while enduring temperatures as high as 1700 degrees Celcius, subjecting the components to high thermal effects and mechanical loads. Every aero-engine manufacturer has been challenged to design and manufacture such blades.>
Global landscape>
Globally, only a few countries can design, develop, test, manufacture, and maintain commercial and military aero-engines. General Electric (US), Honeywell (US), Pratt and Whitney (US), Rolls Royce (UK), Safran (France) and United Engine Corporation (Russia) are the Original Equipment Manufacturers (OEMs) that can build an aero-engine. In contrast, countries like Germany, Japan and Canada have joint ventures. CFM International is one such joint venture between General Electric and Safran, which builds popular CFM56 and LEAP commercial aero-engines. Other notable joint ventures are Engine Alliance, International Aero-Engines, Powerjet, and Eurojet Turbo.>
Also read: As Yet Another Committee Takes Off, There’s No End in Sight to the Indian Air Force’s Woes>
China has invested huge capital and resources in developing military and civil aero-engines but has struggled to build one until now. Multiple reports suggest China’s indigenously developed WS-10 engine powers J-10 fighter aircraft. The state-owned enterprise Aero-Engine Corporation of China (AECC) is actively developing aero-engines for China, including the WS-10, WS-13, and WS-15 for fighter aircraft and the WS-18 and WS-20 for transport aircraft. Despite substantial development, achieving performance and reliability on par with global players is still a huge challenge for China’s aerospace industry.>
India’s growing ecosystem>
HAL is a major manufacturer of aircraft engines in India. It manufactures engines of Russian, US, and British origin under licence. They co-developed a turboshaft engine called Shakti with Safran on Ardiden 1 engine. It has two engine manufacturing units, one in Bangalore, Karnataka and another in Koraput, Odisha. Many private companies manufacture aero-engine components, including Tata Advanced Systems Limited, Reliance Defence, Bharat Forge, International Aerospace Manufacturing Pvt. Ltd (IAMPL), Godrej Aerospace, Mishra Dhatu Nigam Limited (MIDHANI), and other MSMEs.>
Gas Turbine Research Establishment (GTRE) is the key entity developing an indigenous turbofan military aero-engine. It has six decades of experience developing aero-engines. The Ministry of Defence sanctioned the Indigenous engine programme in 1989, allowing the GTRE to design and build turbofan engines, named Kaveri, for Light Combat Aircraft, also known as HAL Tejas. The flagship aero-engine programme for developing the Kaveri engine has fallen short of its design goals. It was intended to produce 81kN and weigh approximately 1000 kg. However, the current thrust is only 70 kN, 13% less than expected, and its weight has overshooted by 12%, reaching 1235 kg. Other concerns are reported regarding its reliability and noise issues. >
Many factors have contributed to the delay and underperformance of the Kaveri Engine. The programme began with the ambitious goal of developing the engine using the existing technological and industrial base in seven years. However, a lack of expertise hindered the process. Compounding these challenges, India’s reliance on Russian facilities to test newly developed engines lead to high costs and long wait times due to insufficient domestic testing infrastructure.>
Another DRDO lab, Aeronautical Development Establishment (ADE), is developing turbojet engines for drones and missiles. National Aerospace Laboratories (NAL) and Research Centre Imarat (RCI), a DRDO lab, are developing an engine for the NAL Rustom-II UAV. HAL’s Aero-Engines Research and Design Centre (AERDC) is developing a turbofan engine for UAVs and a turboshaft engine to replace the Shakti Engine, which powers HAL’s ALH and LUH helicopters. Bharat Forge, an Indian private company, is developing multiple miniature turbojet engines. Startups like Poeir Jets and Raghu Vamsi have been working on micro gas turbines that propel small UAVs. The emerging ecosystem has resulted in numerous developments in aero-engines.>
Future of India’s aero-engine programme>
With nations advancing to sixth-generation fighter aircraft, the engine requirement is evolving. Shifting geopolitical dynamics, especially in the Indo-Pacific region, make it imperative for India to accelerate its effort to indigenise the aero-engine development. Achieving this self-reliance will entail fundamental changes in its institutions, R&D ecosystem, talent development, infrastructure, and private sector participation.>
The execution of the indigenous aero-engine programme has to evolve. Shifting the programme under the Prime Minister’s Office (PMO) and operating it in mission mode would centralise oversight and expedite progress. Transforming the role of GTRE from a solitary entity to an enabling collaborator is essential. With its experience, GTRE can pave the way for the ecosystem towards collaborative development on the Kaveri engine programme. >
Cultivating close partnerships with universities will supplement their scientific and technological research requirements, facilitating knowledge exchange and talent development. This would attract young local scientific and engineering talent while enabling lateral entry for experienced professionals to take up managerial responsibilities. This structure would ensure emerging researchers work under efficient managers and are led by established scientists.>
To complement this, GTRE must work closely with HAL and private industries to provide competitive design, manufacture, and assembly of the engine and its components. HAL’s experience in co-developing engines with Safran will help it use this knowledge to design, develop, and manufacture the Kaveri and upcoming engine programmes. Other emerging private entities venturing into small engines must partner to upgrade their knowledge and experience in building engines, further strengthening India’s private engineering and manufacturing entities.>
Moreover, India must prioritise investment in critical engine testing infrastructure, such as flying engine test beds and high-altitude engine tests. Establishing these as national labs accessible to the entire ecosystem would reduce dependency on foreign nations, lower costs, and expedite the validation of indigenous engines.>
India’s aspiration for self-reliance in aero-engine technology requires a strategic and holistic approach. India can accelerate the realisation of an Indigenous engine by establishing a robust foundation, prioritising institutional transformation, building a collaborative ecosystem, and investing in critical infrastructure. This will reduce dependence on foreign entities and propel India’s aerospace and defence capabilities, ensuring its future strategic autonomy and technological prowess.>
Avinash Shet is a research analyst at Takshashila Institution.>